3 The process-based methodologies
Overview
Process-based project management methodologies follow a systematic process which incorporates creation, management, and improvements. The process aims to align the objectives of the project to those of the organisation, project team, stakeholders, and clients (Goodman 2006). Within this process, all tasks, activities, and objectives must contribute to the outcomes of the project and business strategies. The primary aim is to achieve a common goal, based on collaboration between project team members, stakeholders, and the clients.
Process-based project management ensures that the project team understands the current state, potential improvements, and optimal end-state. This method allows organisations to understand the different requirements of the project to meet the overarching outcomes, and how to best manage the individual processes, tasks, and activities within the project. As per research by Myles and Coats (1995), through process-based project management, organisations are better able to:
- understand the varying client demands, needs and expectations, including how they change over time and in response to environmental factors
- support the response to the identified client expectations
- develop skills and capabilities in the project management domain
- manage their project from end-to-end
- integrate their various projects, programs, and portfolios
- identify and manage the different success and benefit indicators
- link the project outcomes to the organisational goals and objectives.
Within process-based project management, there are 6 commonly identified stages (Myles and Coats 1995), as outlined in Figure 6.

Stage 1: Define the process. Processes need to be clearly identified, precisely documented and shared with the project teams to ensure that they are properly followed and understood. This includes using tools, documentation, stakeholder consultations, agreements, guides for asset management and process diagrams/flow charts. The process should also define the responsibilities and roles of the different team members, including operational needs, reporting requirements and performance expectations.
Stage 2: Identify indicators. Evaluation is a crucial step in the process, including developing, collecting, and monitoring data outlining the performance of the process and team. This ensures that future improvements can be implemented around efficiency, quality, duration, and scheduling. These indicators need to be quantifiable, using comparative data, relevant references, and other supporting data for analysis.
Stage 3: Measure process performance. The current performance of processes needs to be measured to ensure the achievement of objectives and outcomes. This also enables a team to make decisions that support efficiency, evolve over time, and solve complex issues.
Stage 4: Adjust objectives. Check compliance of the process to ensure it is stable and adequate. If it is not, determine how to best improve the processes moving forward.
Stage 5: Improvements. Ongoing improvements and changes will occur to organisational culture, mission and vision statements, and objectives. Therefore, success measurement needs to be considered for all changes.
Stage 6: Implement selected improvements. For improvements as outlined in the previous step, organisational training may be required, as well as ongoing support for team members, and regular monitoring and continuous improvement of processes.
Advantages and disadvantages of process-based project management
There are numerous advantages of applying process-based project management, including improved processes, increased value-adding activities, reduced costs, and strategic alignment to the organisation.
Organisations which follow process-based project management processes see improvements to flexibility, interpersonal relationships between employees, and the reach of the outcomes. Within a process-based methodology, every staff member knows their roles and responsibilities, and they collaborate to achieve the end-state. As a result, use of resources is improved, decreasing overall costs.
Most process-based methods encourage continuous improvements, whereby inefficiencies are identified and removed. Therefore, applying this method to a project and/or an organisation, there is a move away from a hierarchical system. Instead, roles and responsibilities are dictated based on organisational need. Change management also becomes a key area within the planning process. Organisational training needs to be ongoing, ensuring that every employee is part of the process.
Process-based project management methodologies include the following:
- PRINCE2: the main focus is 7 principles, 7 themes, 7 processes.
- Lean Project Management: the main focus is maximum efficiency, minimum waste.
- Six Sigma: the main focus is improvement by eliminating defects/bugs.
- Lean Six Sigma: the main focus is no waste + zero defects.
Let’s explore each of these approaches.
PRINCE2: 7 principles, 7 themes, 7 processes
PRINCE2 is a process-based method for effective project management, and it stands for PRojects IN Controlled Environments. The focus of this method is on breaking a project into smaller components and stages (Axelos 2015; PRINCE2 2022). This is achieved by outlining clear roles and responsibilities and applying the project life cycle using the 7 processes outlined in PRINCE2. Projects should also be broken into logical steps, following a framework that is organised and controlled prior to starting the work, and is maintained and followed throughout the execution (Axelos 2015; PRINCE2 2022). PRINCE2 is based on the following 7 key principles, 7 themes and 7 processes.
Seven Principles
The PRINCE2 method is based on the application of 7 principles (also referred to as guidelines) which are not to be altered. PRINCE2 principles are defined as a mindset. If the project does not meet these principles, it should not be managed through PRINCE2 methodology (Lawton 2015; Bennett 2017; Axelos 2018). These principles, as outlined in Lawton (2015), are:
- Continued business justification. The business case is vital and updated throughout the project to ensure that the project remains viable. Through the business case, if the project ceases to provide value, the project can be terminated early.
- Learning from experience. Maintain a lesson learned register for each project and ensure that the project team uses the logs throughout the project (and reviews registers from previous and concurrent projects).
- Defined roles and responsibilities. Within PRINCE2 there are 4 levels of structure in terms of roles and responsibilities, including program or corporate management, project board, project manager and project management team level. Within the project management team, all the primary stakeholders need to be represented (business, user, and suppliers), along with the roles and responsibilities of the team members themselves.
- Managing through stages. Projects are controlled and planned in stages, moving stage by stage. This includes updating documentation as required, including the business case, risk register, project plan and next steps work breakdown structure.
- Management by exception. Projects using the PRINCE2 method have defined tolerances (6 aspects, defined below) for each objective, outlining levels of authority. If these tolerances are exceeded, the decision needs to be extended to a higher delegation.
- Focus on products/outcomes. The project’s primary focus should be the definition and delivery of products or outcomes, including their quality requirements.
- Tailored to suit project environment. PRINCE2 should be tailored to meet the project needs (for example, environment, size, complexity, importance, scheduling, budget, and risk). Within PRINCE2 the first activity is tailoring within the initiation phase (which is then reviewed at each stage).
Not every principle or component outlined with PRINCE2 is applicable to every project. The components are used to guide the project manager and project team on whether these processes are relevant to the project specifics. A primary element of PRINCE2 is tailoring the needs to a particular project (Lawton 2015).
Six aspects
The 6 aspects are also referred to as the project tolerances and/or performance goals. These are used to quantify the project tolerances or performance expectations that need to be followed and considered as part of the decision-making process (Lawton 2015; Bennett 2017; Axelos 2018). Additionally, these can be referred to as Key Performance Indicators (KPIs). Table 4 outlines the various aspects within PRINCE2.
Table 4. Six aspects of PRINCE2 (Lawton 2015; Axelos 2018)
Tolerance type | Maintained in the project level |
Scope | Project plan, scope of work and scope statement |
Timescale | Project plan, project schedule |
Risk | Risk registers and risk management plan |
Quality | Project quality management plan and KPIs |
Benefits | Business case and KPIs |
Cost | Project plan, budget |
Project benefits can be difficult to determine, especially when related to ensuring that the project remains within cost/budget.
Seven Themes
Themes are the activities which need to be completed at the start of a project. They are used to set a baseline and monitor a project throughout its life cycle. Themes are used to guide how the project should be managed (Lawton 2015; Bennett 2017; Axelos 2018). Therefore, themes are tailored to suit the project needs, depending on the environment, scale, budget, and schedule (Lawton 2015). These are outlined in Table 5.
Table 5. Seven themes of PRINCE2 (Lawton 2015; Axelos 2018)
Theme | Management Products |
1. Business Case | Business Case
Benefits management approach Co-design Governance Stakeholder engagement |
2. Organisation | Communication Management
Advisory group Project team Co-design groups |
3. Quality | Quality register
Quality management plan Key performance indicators Feedback Review current and plan future practices and pathways Identify best practice Stakeholder engagement |
4. Plans | Following steps:
These fit within the:
|
5. Risk | Risk register
Risk management Risk mitigation |
6. Change | Issue register
Change management approach Stakeholder engagement Change approval |
7. Progress | Baseline to measure project success
Reviews of the issue register, quality register, risk register Reporting: checkpoint, highlight report, end stage report, end project report |
Seven Processes
The 7 processes are used to manage a project and identify the roles and responsibilities of the project team members (Lawton 2015; Bennett 2017; Axelos 2018).
- Project start up. This step determines whether the project is viable and includes the project brief, business case and stepping out a plan of the key milestones. Within this step, the project manager is appointed along with the project team (Axelos 2018). This step should provide a clear scope of work to be completed and support the creation of baselines and performance expectations.
- Project initiation. This step requires the definition of the project aspects (for example, scope, cost, schedule, risk, quality, and benefits) (Axelos 2018).
- Direct a project. This step requires ensuring that the decision-makers are accountable throughout (Axelos 2018).
- Control a stage. This step involves controlling how each individual stage will be managed, following the work breakdown structure, the project plan and schedule. The project manager is responsible for assigning work, and ensuring it is completed and meets the requirements (Axelos 2018). These should be reviewed; ongoing checks need to be in place to verify and compare the progress of the project work against the project plan and consider the issues and risks that have occurred and their resulting impact.
- Manage product/outcome delivery. This step involves managing the delivery of the project product or outcomes, controlling the work being completed and the performance of the project team (Axelos 2018). For the project manager and project team there should be formal requirements for their performance, their acceptance criteria, steps for execution and delivery of the project work.
- Manage stage boundary. This step is broken into 2 parts. First, the project manager is responsible for providing updates to the project boards outlining the performance, updates or changes to documentation, and creating next steps plans (as required) (Axelos 2018). Second, information provided by the project manager to the project board is used to provide understanding of what they are approving or how work is progressing (Axelos 2018). Overall, this step is used to document transitioning or moving between stages.
- Project closure. This step involves the formal closure of the project, transitioning to business as usual and evaluation of the benefits/performance (Axelos 2018).
In sum, PRINCE2 is a commonly used process-based project management methodology. PRINCE2 project management methodology offers significant benefits to project managers, project sponsors, and project team members within an organisation and for the organisation more broadly. These benefits link back to the fact that the project is more controllable using resources and can manage the business and risks associated with the project more efficiently.
Lean project management: maximum efficiency, minimum waste
Lean project management is often referred to as less of a project management tool and more of a mindset for driving continuous improvement. The lean method is based on experiences within the Toyota Production System (TPS) and is often referred to as Toyota’s Lean Method. It is based on applying lean manufacturing principles to managing projects (Womack et al. 1990; Womack and Jones 1996; Moujib 2007). The method focuses on reducing waste across all business processes, resulting in cost and lead-in time reductions and quality improvements.
As the basis of Lean management is continuous improvement, it fits within the broader Agile project management environment. This is due to its overarching flexibility and adaptability to change. The primary focus is delivering value to clients/customers and broader stakeholders.
Lean manufacturing: Toyota Production System
After the 1973 energy crisis, Toyota was the only organisation that managed to resist foreclosure. It did so by changing the way in which it worked to be more efficient and effective. Through implementing a cultural shift within their organisation and empowering its workforce, Toyota was able to undertake a continuous improvement process (Womack et al. 1990; Womack and Jones 1996; Moujib 2007). Encouraging its employees to identify inefficiencies and overcome them through implementing new ways of working (Womack et al. 1990; Womack and Jones 1996; Moujib 2007) led to improvements in its product quality and client satisfaction, and a reduction in cost and lead-times.
This process was a breakthrough for mass production, which started to move towards lean production – from a push system to a pull system.
Lean benefits
The Lean methodology uses less of everything, compared to most other mass production processes (Womack et al. 1990:256). Benefits outlined in the literature include:
- reduced lead-in times
- lower inventory and storage costs (due to less over-production)
- decreased overall costs
- productivity and efficiency improvements
- increased quality
- improved client satisfaction.
3Ms of Lean
‘To be lean is to provide what is needed, when it is needed, with the minimum number of materials, equipment, labor, and space’, (Moujib 2007). Within Lean manufacturing, there are three types of waste: Muda, Muri, and Mura (commonly referred to as the 3Ms) (Moujib 2007).
- Muda includes activities which consume resources without providing additional value.
- Muri includes overuse of equipment or employees.
- Mura outlines operational ‘unevenness’, based on decreased long-term efficiency and productivity.
The overarching aim of Lean project management is to reduce the 3Ms within the project process.
Principles of Lean Thinking
A primary element of Lean project management is the application of 5 principles (outlined in Figure 7). The first step is to understand how to apply the 5 principles to your project (Womack et al. 1990; Womack and Jones 1996; Moujib 2007).
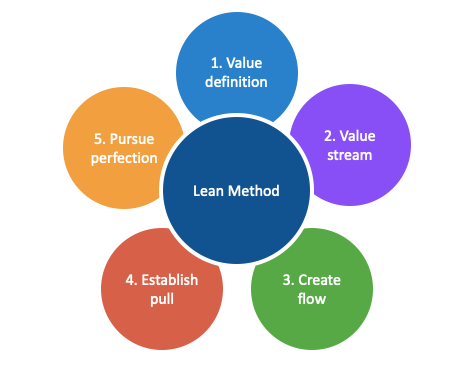
The 5 principles are:
1. Specify value in the eyes of the customer
Specifying value is the first lean principle. This principle requires defining the value of a product, service, or outcome (Womack et al. 1990; Womack and Jones 1996; Shook and Rother 1999; Morgan 2002; Moujib 2007). Value ensures that the outcome is provided to clients at the right time, based on the right price and to the requirements of the client (Womack and Jones 1996). Value should be outlined in the client’s words. The challenge of Principle 1 is being able to focus on what the client is willing to pay and their overarching needs.
2. Identify the value stream for each product
Identifying the value stream is the second lean principle. The value stream can be defined as all the actions within the process that are required to bring about the outcome or product to the client (Womack et al. 1990; Womack and Jones 1996; Shook and Rother 1999; Morgan 2002; Moujib 2007). This includes all steps from design, planning, testing, and launching. The flow should also outline the different value-added and non-value-added processes (Morgan 2002).
The first step in applying Principle 2 is creating a value stream map. This should reflect the current state of how processing is occurring within the organisation, or the steps taken to reach an outcome (Morgan 2002). Once completed, this map needs to be analysed to identify where there is waste and how value can be created. After this has been completed, the future-state map is documented, and it is the representation of how the process needs to operate to reduce waste.
Using these process maps, an improvement plan is generated. This plan will support the transformation from current to future state.
3. Make value flow by eliminating waste
Principle 3 involves the flow of value through the elimination of waste. After defining the value, identifying the value stream and considering the improvement plan, the next step is to create continuous flows (Womack et al 1990; Womack and Jones 1996; Shook and Rother 1999; Morgan 2002; Moujib 2007). This requires eliminating backflows, reworks, wasted work, interruptions, and scrap. The elimination process should involve removing stoppages throughout the process and ensuring that all value streams identified fall within 3 categories:
- Value-Added Work: essential to producing the outcome, product, or service. The aim is to maximise work that fits within this category, as the aim is to provide client value (Form, Fit, Function) (Morgan 2002).
- Value-Enabling Work: work that can be potentially eliminated in the future (based on identified improvements) but cannot be eliminated immediately. In the current state, this work is necessary (Morgan 2002). This incorporates different components, including technology, environment, culture, and others. The aim is to identify waste in this section and minimise work within this category.
- Non-Value-Added Work: work which can be eliminated quickly as it does not flow on to improvements in other areas (Morgan 2002). This section outlines the work that is not needed, defined as pure waste. The aim is to eliminate all work within this category.
In addition to the 3 categories of waste, all the waste (‘pure’ or ‘necessary’) identified can be classified within one of the following 7 types (Womack et al 1990; Womack and Jones 1996; Shook and Rother 1999; Morgan 2002; Moujib 2007):
- Over production: producing more than is necessary before it is required.
- Waiting: non-work time waiting for approval, supplies, parts, etc.
- Transportation: effort wasted on transportation of materials, parts, or finished goods into or out of storage or between processes.
- Over processing: undertaking more work than required (customer requirements) or double the work.
- Inventory: holding excess inventory of raw materials, parts in process or finished goods.
- Motion: wasted motion or actions to pick up or stack parts.
- Defects: reworks or repairs required due to inferior quality.
4. Let the customer pull the flow
Principle 4 is around letting the client pull the flow. This principle presents a challenge, specifically how to avoid delivering value prior to the client’s customer request (Morgan 2002) and ensuring that the outcomes provided do not exceed the initial and agreed upon scope. By letting the client pull the flow, the implementation is based on the just-in-time system, whereby the client signals the need for the item or outcome triggering the next steps required.
5. Continuously improve in the pursuit of perfection
The fifth and final principle is the pursuit of perfection through continuous improvement. This requires a process of improvement built into the business as usual and within the culture (Morgan 2002). The pursuit is endless, and as a result all activities should be questioned as to the value they add. Perfection may never be achievable; however, the aim should be to get as close as possible.
In sum, Lean project management is a process-based project management methodology. This methodology is also referred to as a mindset around the improvements within an organisation. The focus is on improving efficiency, reducing waste, and increasing productivity. There are many benefits associated with the application of Lean methods, including better product outputs and quality and improving the overall organisational efficiency and allocation of resources. Lean methods encourage innovation and quality controls.
Six Sigma: improvement by eliminating defects/bugs
Six Sigma uses a set of techniques and tools for process improvement. The purpose of Six Sigma is to identify improvements to quality in manufacturing through detecting and removing causes of defects, aiming to minimise variability in outputs. To achieve this, Six Sigma uses statistical quality management methodologies (Harry 1988; De Feo and Barnard 2005; Gygi et al. 2005; Kwak and Anbari 2006). Each project follows a set methodology, based on specific value targets (for example, reduction in pollution, improvements to client satisfaction, decreased cost of production).
The term originates from statistical modelling within manufacturing processes, the maturity of which is described through a ‘Sigma rating’ which indicates yield or number of defect-free products (Harry 1988; De Feo and Barnard 2005; Gygi et al. 2005; Coryea et al. 2006; Kwak and Anbari 2006). In technical terms, it relates to how many standard deviations within the normal distribution the percentage of defect-free outcomes equates to.
Six Sigma: Motorola manufacturing
Six Sigma was developed by Motorola, who set Six Sigma as the goal for their manufacturing. The process was developed to promote quality outcomes within an organisation, with a focus on the elimination of defects (Harry 1998). The term was coined in 1985 by Bill Smith and trademarked by Motorola in 1987 (Harry 1998). It has also been defined as an attitude, whereby making outcomes defect-free should be the aim of all employees.
Six Sigma components
This method requires the following components (Harry 1988; Kwak and Anbari 2006):
- Continuous improvements are to be implemented as part of the process, in order to create a stable and predictable output. This stability is vital to business success.
- Characteristics within manufacturing and business processes need to be defined, measured, analysed, improved, and controlled.
- The entire organisation should be committed to achieving ongoing quality improvement – this is especially important for higher level leaders.
There are a number of features within Six Sigma which set it apart from similar methods:
- The focus is on achieving measurable financial returns.
- Leadership and support from management is vital.
- Verifiable data-driven decisions are required to remove guesswork.
The focus of Six Sigma is eliminating defects and reducing variation. The primary goal is to improve processes, so an organisation should determine the appropriate Sigma level for every one of their processes and aim to achieve these. It is important that management is clear on the areas for improvement and how they will be attained.
Methodologies
Six Sigma projects follow two project methodologies (De Feo and Barnard 2005), as follows.
-
DMAIC
This is used for projects which aim to improve an existing business process. It follows 5 key phases (De Feo and Barnard 2005) (see Figure 8).

- Define the system. Document and understand the needs of the client and what they require and use this data to develop the project scope and goals.
- Measure the current process and use it as a baseline.
- Analyse data and identify where possible the different causes and effects. Highlight the relationships between the different factors, then, once all factors have been considered, seek out the root cause of the defects.
- Improve the current process, based on data analysis techniques and mapping future-state processes. It is recommended that organisations use pilot testing to understand the impact of proposed changes.
- Control future-state processes by ensuring deviations from target are corrected before they cause defects. This requires implementing quality control systems (for example, statistical controls), and continuously monitoring the process. This entire process should be ongoing and repeated until desired quality levels are obtained.
-
DMADV
This is used for projects which aim to create new outcomes, products, or process designs. The process is also referred to as Design For Six Sigma (DFSS). It follows 5 key phases (De Feo and Barnard 2005) (see Figure 9).

- Define or design project goals which meet the client requirements, and new or existing organisational strategies.
- Measure and identify all the distinctive characteristics which are Critical to Quality, and can be used to measure the outputs, risks, and capabilities.
- Analyse the proposed future state and develop proposals for potential alternatives that can support improvements.
- Design an improved outcome, based on the analysis completed in the analyse step.
- Verify the design using test runs or pilots, implement the process into business as usual and complete the handover.
Benefits to Six Sigma
Organisations can benefit from applying Six Sigma methodology to their business and projects in many ways (Harry 1988; De Feo and Barnard 2005; Gygi et al. 2005; Coryea et al. 2006; Kwak and Anbari 2006), including the following:
- Reduction in operational costs. The application of Six Sigma can provide organisations with a future-state process map which highlights inefficiencies and reduces the exposure to risks, making the organisation more efficient and effective at delivering its outcomes.
- Improved efficiency or timeliness. This methodology improves the efficiency of processes, encouraging timeliness in delivering products or services on time.
- Improved accuracy, controls, and policy compliance. It helps to improve accuracy through reducing Defects-Per-Million-Opportunities (DPMO) across the process value stream. The DPMO is a probabilistic measure of error rate and takes into consideration actual and probable defects in every opportunity.
- Improved customer service. Organisation corporate is significantly impacted by client interactions. By applying Six Sigma, organisations can better understand client experience, understand what is causing different experiences and minimise dissatisfaction.
- Improved cash flow. The primary improvement gained by applying Six Sigma relates to improvements in sales, which results in cash flow improvement.
- Improved regulatory compliance. There are 3 primary types of regulatory compliance: financial and audit, information technology, and legal. The Six Sigma project type will dictate which of these will be the focus and what kinds of defects or efficiencies can be identified.
In sum, Six Sigma is a process-based project management methodology. This method provides organisations and project managers with several tools which support the improvement of business processes and their capability. Like Lean, the purpose is to improve performance of team members including outputs, while decreasing variations in the process to achieving an outcome. This in turn leads to reduction in defects and supports improving profits, team morale and quality outcomes.
Lean Six Sigma: no waste + zero defects
Lean Six Sigma is defined as a collaborative team effort, based on improving overarching performance through the systematic removal of waste (George 2002). It is a combination of Lean project management and the Six Sigma method, which aims to eliminate 8 distinct types of waste (referred to as muda) (George et al. 2003). Therefore, the principles of Lean Six Sigma are aimed at improving both quality processes and efficiency.
Waste
Waste can be defined as anything other than the minimum required levels of materials, equipment, parts, space and employees which are essential to complete the product (Summers 2011). The several types of waste are outlined below (Skmot 2017):
- Defects: a product that is unfit for use, requires disposal or reworking. This costs money and time to address.
- Over-production: excess products or those made or purchased before they are required.
- Waiting: delays caused by waiting for material or equipment or conversely unused equipment.
- Non-used talent: wasting human potential and skills, where employees are not empowered to provide feedback or obtain training and skills improvement.
- Transportation: unnecessary or excess movement of people, tools, equipment, products or materials.
- Inventory: excess products and materials that go unprocessed. It could cause items to become unnecessary before the start of its life cycle usage, storage costs increase or damage could occur to the materials.
- Motion: unnecessary movement by people, whereby excessive motion wastes time and can cause injury.
- Extra-processing: doing more work than required to complete a task.
Three key elements of Lean Six Sigma
There are 3 primary elements that need to be understood and considered as part of the application of Lean Six Sigma (George 2002; Summers 2011):
- Customers: These need to be at the centre of everything that an organisation does and support the development of the outcome. Customers are primary stakeholders with a significant interest in obtaining products which are of the highest quality but the cheapest price.
- Processes: Business processes require a rework or evaluation, changing to an outside-in approach based on the value chain. Customers pay for products which are defect-free. Therefore, organisations using Lean Six Sigma focus primarily on high quality products and outputs.
- Employees: Clear business processes are required across all levels of the organisation. Transformation needs to be part of the organisational culture.
Within Lean Six Sigma, innovation stems from need. Need is driven from customer expectations and requirements. Organisations must constantly evolve and this includes developing innovative solutions, with the aim of pre-empting the market needs.
Lean Six Sigma principles
There 5 fundamental principles of Lean Six Sigma (George 2002; Summers 2011) (see Figure 10).
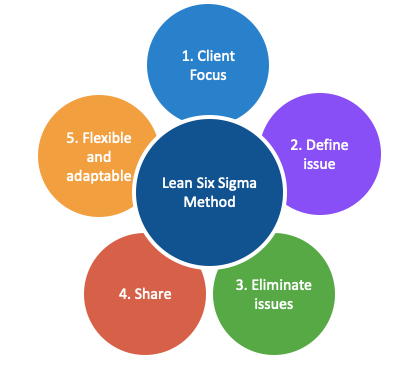
- Customer focus. Define what ‘quality’ and ‘satisfaction’ mean to customers and align business processes with the employees and skills required to achieve the goals.
- Define roadblocks to consistent quality. Undertake an assessment of the organisational priorities which aim to meet customers’ and stakeholders’ expectations. The organisational problems and priorities need to be well defined, and this can be supported by qualitative and quantitative data.
- Eliminate inefficiencies. Remove non-value added and value-added steps within business processes. Through applying Lean Six Sigma, organisations can eliminate waste, simplify processes and offerings, or automate where possible. The aim is to measure the outcomes and improve as needed.
- Communication and employee alignment. Ongoing communication and training should be implemented across the organisation, establishing a cultural change of collective problem-solving. This cultural change should also be encouraged down from the leadership and managerial levels to the employees.
- Be flexible and adaptable. Organisations, including their employees, need to be responsive to change. This should include changes to organisational structure and management strategies, to enable responsiveness to the market.
Benefits of Lean Six Sigma
The implementation of Lean Six Sigma methodology should influence the entire organisation’s approach to delivering customer outcomes (George 2002; Summers 2011). There are a multitude of benefits that the application can provide, including the following:
- Talent and capability development. Using Lean Six Sigma requires ongoing development of employees’ capabilities. As a result, there is an enhanced focus on talent development and continuous learning built into the organisational culture.
- Quality delivery through efficient business processes. Business processes are supported through data-driven decision-making and increased transparency. Quality comes from the client-centric focus which ensures that customer voices are heard and that future designs will meet the changing market.
- Scalable across sectors. Lean Six Sigma can be applied broadly across industries, with successful application seen across retail, IT, healthcare, and other sectors.
- Basis for technology deployment. Lean Six Sigma aims to drive continuous improvement. There are many scenarios where it has supported digital transformation efforts, alongside broader business transformation strategies.
- Enhancement of brand value. Clients trust organisations that respond to their issues and challenges in a timely way. Lean Six Sigma encourages an organisational culture whereby people and processes are based on enhancing brand.
In sum, Lean Six Sigma is another process-based project management methodology. Organisations that use this methodology often identify improvements to their overall client experience and as a result improved client loyalty. These improvements are also evident across the organisation, with improvements to their internal efficiencies, processes and team members, along with increased profitability. Like Lean and Six Sigma, this process-based methodology aims to prevent defects in products or outcomes, reduce costs and remove waste wherever possible.
Test your knowledge
Key Takeaways
- Process-based project management methodologies follow a systematic process which incorporates development, management, and improvements.
- The focus of the PRINCE method is on breaking a project into smaller components and stages.
- Lean project management is often referred to as less of a project management tool, and more of a mindset for driving continuous improvement.
- The purpose of Six Sigma is to identify improvements to quality in manufacturing through identifying and removing causes to defects and aims to minimise variability in outputs.
- Lean Six Sigma is defined as a collaborative team effort, based on improving overarching performance through the systematic removal of waste.
References
Axelos (2015) Prince2 Agile, Stationary Office, United Kingdom.
Axelos (2018) Directing successful projects with PRINCE2®: the essential guide for project board members (managing successful projects With PRINCE), Stationary Office, United Kingdom.
Bennett N (2017) PRINCE2 handbook: managing successful projects with PRINCE2, Stationary Office, United Kingdom.
De Feo JA and Barnard W (2005) JURAN Institute’s Six Sigma breakthrough and beyond: quality performance breakthrough methods, Tata McGraw-Hill Publishing Company Limited.
George ML, Rowlands D and Kastle B (2003) What is Lean Six Sigma?, McGraw-Hill Education, accessed 3 August 2022. https://archive.org/details/whatisleansixsig00geor
George ML (2002) Lean Six Sigma: combining Six Sigma quality with lean production speed, McGraw-Hill Education.
Goodman AF (2006) Process-based software project management, CRC press, United States.
Gygi C, DeCarlo N and Williams B (2005) Six Sigma for dummies, Wiley Publishing, Hoboken, NJ.
Harry MJ (1988) The nature of six sigma quality, Motorola University Press, Rolling Meadows, Illinois.
Kwak YH and Anbari FT (2006) ‘Benefits, obstacles, and future of six sigma approach’, Technovation, 26.
Lawton I (2015) PRINCE2 made simple, 6th edn, P2MS Press, United Kingdom.
Myles DT and Coats ML (1995) ‘Process-based project management systems’, PM Network, 9(6):10–14.
Morgan J (2002) High performance product development: a systems approach to a lean product development process, Doctoral thesis in Industrial and Operations Engineering, University of Michigan.
Moujib A (2007) ‘Lean Project Management’ [conference presentation], PMI® Global Congress 2007, EMEA, Budapest, Hungary, Project Management Institute, Newtown Square, PA.
PRINCE2 (2022) What is PRINCE2?, PRINCE2, accessed 3 August 2022. https://www.prince2.com/aus/what-is-prince2
Shook J and Rother M (1999) Learning to see: value stream mapping to add value and eliminate muda, The Lean Enterprise Institute, Brookline, MA.
Skmot N (5 August 2017) ‘The 8 wastes of lean’, The Lean Way, accessed 02 June 2022. https://theleanway.net/The-8-Wastes-of-Lean
Summers DCS (2011) Lean Six Sigma: process improvement tools and techniques, Prentice Hall, New Jersey.
Womack J and Jones D (1996) Lean thinking: banish waste and create wealth in your corporation, Simon & Schuster, New York.
Womack J, Jones D and Roos D (1990) The machine that changed the world: the story of lean production, HarperCollins, New York.